MDPE pipes, known for their durability and flexibility, are in high demand due to their suitability for various applications. This article explores the MDPE pipe manufacturing process, emphasizing the importance of quality and efficiency. It covers selecting high-quality raw materials, essential equipment, and facility setup. The manufacturing process, including extrusion, cooling, and cutting, is detailed. Quality control and regular testing ensure excellence. The article also highlights efficiency boosters, such as waste reduction and automation, and discusses innovations and future trends. Safety protocols, employee training, and emergency preparedness are essential for a safe work environment. By following these guidelines, manufacturers can produce superior MDPE pipes and thrive in a competitive market.
MDPE Pipe Manufacturing Process: Top Tips for Success
Introduction MDPE Pipe Manufacturing Process
The demand for MDPE (Medium-Density Polyethylene) pipes has surged in recent years, becoming a staple in various industries due to their durability, flexibility, and cost-effectiveness. As infrastructure projects expand globally, the need for high-quality piping solutions is more critical than ever. This article delves into the intricacies of the MDPE pipe manufacturing process, offering essential tips to elevate quality and efficiency. By mastering these aspects, manufacturers can stay ahead in a competitive market and deliver superior products to their customers.
The Rising Demand for MDPE Pipes: A Quick Overview
In an era where urbanization and industrialization are on the rise, MDPE pipes have found widespread applications, from water supply systems to gas distribution networks. Their resistance to corrosion and ability to withstand harsh environmental conditions make them a preferred choice over traditional materials like steel and iron. This rising demand is not just a fleeting trend; it signifies a shift towards more sustainable and reliable infrastructure solutions.
Why Quality Matters in MDPE Pipe Manufacturing
Quality is the cornerstone of any manufacturing process, and MDPE pipe production is no exception. The integrity of these pipes can directly impact public safety and operational efficiency. Poor-quality pipes may lead to leaks, system failures, and costly repairs. Therefore, adhering to stringent quality standards is not merely a regulatory requirement but a business imperative. Manufacturers who prioritize quality assurance can build a reputation for reliability and gain a competitive edge.
The Importance of Efficiency in Production Processes
Efficiency in production processes translates to cost savings, reduced waste, and faster time-to-market. In MDPE pipe manufacturing, efficiency can be achieved through meticulous planning, automation, and continuous process improvement. Efficient operations minimize downtime, optimize resource utilization, and enhance overall profitability. For manufacturers, achieving a balance between speed and quality is the key to success.
Understanding MDPE: The Basics
What is MDPE? An Overview of Medium-Density Polyethylene
MDPE, or Medium-Density Polyethylene, is a thermoplastic polymer characterized by its moderate density and crystalline structure. It falls between high-density polyethene (HDPE) and low-density polyethene (LDPE) in terms of density. This unique composition imparts MDPE with excellent impact resistance and flexibility, making it ideal for a wide range of applications.
Key Properties of MDPE That Make It Ideal for Piping
MDPE’s properties, such as its high chemical resistance, low permeability to gases, and robust mechanical strength, make it an ideal material for piping systems. Its flexibility allows it to withstand ground movements and temperature variations without cracking. Furthermore, MDPE is lightweight, making it easy to transport and install, which reduces overall project costs.
Common Applications of MDPE Pipes
MDPE pipes are extensively used in various industries, including water supply, gas distribution, and sewage systems. They are also utilized in agricultural irrigation, telecommunications ducting, and fire protection systems. The versatility of MDPE pipes stems from their durability and ability to resist environmental stressors, making them a reliable choice for both residential and industrial applications.
Preparing for Manufacturing: Setting the Stage
Selecting the Right Raw Materials: Ensuring High-Quality Output
The quality of MDPE pipes begins with the selection of raw materials. High-quality polyethene resins with appropriate additives ensure that the final product meets the desired specifications. Manufacturers must source raw materials from reputable suppliers and perform rigorous testing to verify their quality. Using inferior materials can compromise the pipe’s performance and longevity.
Equipment Essentials: Must-Have Machines and Tools
MDPE pipe manufacturing requires specialized equipment, including extruders, cooling tanks, cutters, and coilers. The extruder is the heart of the operation, responsible for melting and shaping the polymer. Cooling tanks help solidify the pipes, while cutters ensure precise lengths. Coilers or winders are used for winding the pipes for storage and transportation. Investing in advanced, high-efficiency machinery can significantly enhance production capacity and product quality.
Facility Setup: Creating an Optimal Production Environment
An optimal production environment is crucial for the efficient manufacturing of MDPE pipes. This involves proper layout planning, adequate ventilation, and maintaining a clean workspace. Temperature and humidity control are vital to prevent material degradation. Additionally, a well-organized facility facilitates smooth workflow and minimizes the risk of accidents.
The Manufacturing Process: From Start to Finish
Step-by-Step Guide to the MDPE Pipe Extrusion Process
The MDPE pipe manufacturing process begins with the extrusion of polyethene pellets. These pellets are fed into the extruder, where they are heated and melted. The molten polymer is then forced through a die to form the pipe’s shape. The pipe is subsequently cooled in water tanks, solidifying its structure. After cooling, the pipe is cut to the desired lengths and coiled or stored as needed.
Cooling and Calibration: Achieving Precise Pipe Dimensions
Cooling and calibration are critical stages in the production process. The pipes must be cooled evenly to prevent warping and ensure uniform wall thickness. Calibration involves adjusting the pipe dimensions to meet specific standards. Accurate calibration is essential to maintain consistency across batches and ensure that the pipes fit correctly during installation.
The Role of Cutting and Marking in Quality Assurance
Cutting and marking are essential for ensuring that each pipe segment meets length specifications and is easily identifiable. Automated cutters provide precise, clean cuts while marking machines imprint essential information, such as the manufacturer’s name, production date, and pipe specifications. This information is crucial for traceability and quality assurance.
Quality Control: Ensuring Excellence
Implementing Stringent Quality Checks at Every Stage
Quality control is an integral part of the MDPE pipe manufacturing process. Implementing stringent checks at every stage—from raw material inspection to final product testing—ensures that the pipes meet industry standards and customer expectations. Quality control measures include visual inspections, dimensional checks, and mechanical tests.
Common Defects in MDPE Pipes and How to Avoid Them
Common defects in MDPE pipes include surface imperfections, inconsistent wall thickness, and internal voids. These defects can arise from improper material handling, equipment malfunctions, or suboptimal processing conditions. Preventing these issues requires careful monitoring, regular equipment maintenance, and adherence to best practices in production.
The Importance of Regular Testing and Inspections
Regular testing and inspections are vital to maintaining the quality of MDPE pipes. This includes hydrostatic pressure tests, tensile strength tests, and environmental stress crack resistance tests. These tests validate the pipe’s performance and durability, ensuring they can withstand operational demands. Consistent testing also helps identify potential issues before they escalate into significant problems.
Efficiency Boosters: Streamlining Your Process
Tips for Reducing Waste in Production
Reducing waste is a key factor in enhancing production efficiency and sustainability. This can be achieved through better material management, process optimization, and recycling. Implementing lean manufacturing principles, such as minimizing excess inventory and eliminating non-value-added activities, can significantly reduce waste and lower costs.
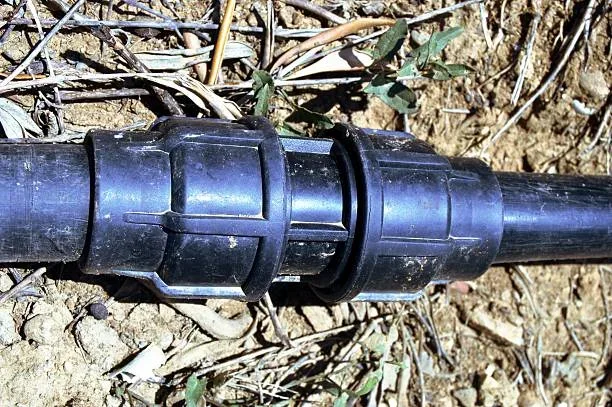
How to Optimize Energy Usage in Manufacturing
Optimizing energy usage is crucial for reducing operational costs and minimizing environmental impact. Manufacturers can achieve this by investing in energy-efficient equipment, utilizing renewable energy sources, and implementing energy management systems. Additionally, regular energy audits can identify areas for improvement and help optimize energy consumption.
Leveraging Automation for Enhanced Efficiency
Automation is a powerful tool for enhancing efficiency in MDPE pipe manufacturing. Automated systems can handle repetitive tasks with precision, reducing human error and increasing production speed. From material handling to quality control, automation can streamline processes, improve accuracy, and free up human resources for more complex tasks.
Innovations and Advancements in MDPE Pipe Manufacturing
Exploring New Technologies in MDPE Pipe Production
The MDPE pipe manufacturing industry continually evolves, with new technologies emerging to improve product quality and process efficiency. Innovations such as advanced extrusion techniques, real-time monitoring systems, and smart manufacturing solutions are revolutionizing the industry. Embracing these technologies can give manufacturers a competitive edge and open new market opportunities.
Sustainable Practices: Going Green in Manufacturing
Sustainability is becoming a critical consideration in MDPE pipe manufacturing. From using recycled materials to reducing energy consumption, manufacturers are adopting green practices to minimize their environmental footprint. Implementing sustainable practices not only benefits the environment but also appeals to eco-conscious consumers and can lead to cost savings.
Future Trends: What’s Next for MDPE Pipes?
The future of MDPE pipe manufacturing holds exciting possibilities. Trends such as the development of bio-based polymers, advancements in pipe performance, and the integration of smart technologies are set to shape the industry. Staying ahead of these trends requires continuous innovation and a proactive approach to adopting new technologies and practices.
Challenges and Solutions: Overcoming Common Hurdles
Dealing with Material Variability: Best Practices
Material variability can pose significant challenges in MDPE pipe manufacturing. Differences in raw material quality, batch inconsistencies, and supplier variations can impact product performance. To mitigate these issues, manufacturers should establish strong relationships with reliable suppliers, conduct thorough material testing, and maintain detailed records of material properties.
Troubleshooting Production Line Issues
Production line issues, such as equipment malfunctions, process inconsistencies, and quality deviations, can disrupt manufacturing operations. Effective troubleshooting involves identifying the root cause of the problem, implementing corrective actions, and preventing recurrence. Regular maintenance, employee training, and process audits can help address these challenges and ensure smooth operations.
Ensuring Consistent Quality Across Batches
Maintaining consistent quality across batches is crucial for customer satisfaction and brand reputation. This requires strict adherence to quality control procedures, comprehensive documentation, and continuous improvement efforts. Implementing a robust quality management system can help manufacturers standardize processes, monitor quality metrics, and ensure that every batch meets the required specifications.
Safety First: Best Practices for a Safe Manufacturing Environment
Essential Safety Protocols for MDPE Pipe Manufacturing
Safety is a top priority in MDPE pipe manufacturing. Essential safety protocols include proper handling and storage of raw materials, regular equipment inspections, and adherence to safety guidelines. Personal protective equipment (PPE) should be provided to all employees, and safety drills should be conducted regularly to ensure preparedness for emergencies.
Training and Education: Equipping Your Team for Success
A well-trained workforce is essential for maintaining safety and efficiency in the manufacturing environment. Ongoing training programs should cover equipment operation, safety procedures, and quality control measures. By investing in employee education, manufacturers can empower their teams to perform their roles effectively and contribute to the company’s success.
Emergency Response Plans: Being Prepared for the Unexpected
Having a comprehensive emergency response plan is crucial for managing unexpected incidents, such as equipment failures, natural disasters, or workplace accidents. The plan should outline clear procedures for evacuation, communication, and emergency medical care. Regular drills and reviews of the plan can ensure that all employees are prepared to respond swiftly and effectively in case of an emergency.
Conclusion
Recap: The Key Takeaways for a Successful MDPE Pipe Manufacturing Process
In conclusion, the MDPE pipe manufacturing process involves a series of intricate steps, from raw material selection to quality control. By prioritizing quality, efficiency, and safety, manufacturers can produce high-quality pipes that meet industry standards and customer expectations. The insights provided in this article offer valuable guidance for optimizing the manufacturing process and achieving success in this competitive industry.
The Path Forward: Implementing Our Tips for Success
Implementing the tips and best practices outlined in this article can help manufacturers streamline their operations, reduce costs, and improve product quality. Continuous improvement and innovation are key to staying ahead in the rapidly evolving MDPE pipe manufacturing industry. By embracing new technologies and sustainable practices, manufacturers can enhance their competitiveness and drive long-term growth.
Final Thoughts: Achieving Excellence in MDPE Pipe Manufacturing
Achieving excellence in MDPE pipe manufacturing requires a holistic approach that encompasses quality assurance, operational efficiency, and a commitment to safety. By focusing on these critical aspects, manufacturers can deliver superior products, build strong customer relationships, and establish themselves as leaders in the industry. The journey to excellence is ongoing, and with the right strategies and mindset, success is within reach.