HDPE Butt-Fusion Welding Machines
HDPE Butt Fusion Welding Machine
High Density Polyethylene Welding Machine
In the realm of poly welding, particularly employing the HDPE butt fusion welding method, the indispensable role of butt welders cannot be overstated. These devices execute the critical tasks of scraping, heating, and flawlessly fusing HDPE pipes.
Butt welders most commonly come in two basic forms: electric hydraulics and manual hydraulics. Other than self-contained welders, all butt welders require a stable power source. This power is used for the proper operation of the heater plate and milling cutter/scraper components. For electric hydraulic butt welders, the same power source also drives the hydraulic system, which holds the pipe firmly in position during the scraping, heating, and cooling processes.
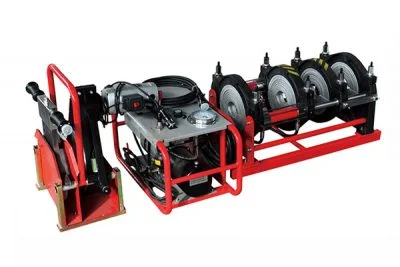
For those embarking on on-site poly welding activities where access to a dependable power supply is a challenge, NEWTECH offers an ingenious solution. We provide portable generators meticulously designed to seamlessly complement poly welding equipment, ensuring a reliable power source in any location.
Discover the diverse range of Butt Welders available from NewTech Industries, each accompanied by its corresponding technical specifications. In the pursuit of the best HDPE pipe welding experience, our equipment stands out for its reliability, efficiency, and precision. Whether you’re working with PVC Pipe or PPRC Pipe, our solutions are tailored to meet the demands of diverse applications, providing a seamless welding experience on-site.
Features of Butt-Fusion Welding
- Seamless Joint Formation: Butt-fusion welding creates smooth, continuous joints by fusing the ends of thermoplastic pipes, ensuring strong and reliable connections.
- Strong & Leak-Proof Performance: The process delivers highly durable, leak-resistant joints that help maintain the integrity of the entire piping system.
- Compatible with Multiple Thermoplastics: Suitable for HDPE, PP, PVC, and other thermoplastic materials, making it ideal for a wide range of piping applications.
- Flexible for Various Pipe Sizes: Designed to handle different pipe diameters, offering great versatility for both small-scale and large-scale projects.
- Precise Temperature & Pressure Control: The welding process uses accurately regulated temperature and pressure to achieve perfect fusion and high-quality joints.
- Long-Lasting Durability: Butt-fusion welds produce joints that are built to last, helping extend the service life of your piping systems.
- Ideal for Above-Ground & Underground Use: Suitable for installations in diverse environments, from above-ground structures to buried pipelines in demanding conditions.
Key Specs: Butt-Fusion Welding Machine
- Operating Temperature Range: Our machines are engineered to operate within an optimal temperature range to ensure clean, consistent pipe fusion.
- Advanced Pressure Control: Built-in pressure systems apply the correct force during welding to produce joints that are both strong and dependable.
- Wide Pipe Size Compatibility: Supports a broad range of pipe diameters to meet the needs of different industrial and construction projects.
- Efficient Heating Plate Design: The heating plate’s dimensions are carefully chosen to ensure even heat distribution and efficient welding.
- High-Quality Heating Plate Materials: Made from durable, heat-resistant materials that ensure stable temperatures and compatibility with various thermoplastics.
At NewTech Industries, we understand the critical importance of reliable butt fusion welding machines in poly welding applications. Our range of HDPE butt fusion welding machines is designed to meet the diverse needs of our customers, ensuring seamless joint creation, strong and leak-free connections, and compatibility with various thermoplastics. With precise temperature and pressure control, our machines deliver durable and long-lasting joints suitable for both above-ground and underground installations. Whether you’re working with HDPE, PVC, or PP pipes, our butt fusion welding machines offer versatility, efficiency, and precision. Explore our range of machines and technical specifications to find the perfect solution for your welding needs.
160 mm Butt Welding – Butt Fusion Machine (Electric Hydraulic):
Buy this HDPE butt fusion welding machine 160 mm butt fusion welder for welding HDPE pipe between 63 mm and 160 mm diameter in electric hydraulic mode. For use in the field, you may need a 5.9 kVA portable generator.
The 160 mm butt welder comes complete with an extractable heating plate, extractable milling cutter, electro-hydraulic gear case, heating plate and milling cutter support, tool kit, and stub end device (spider).
** set of inserts OD 63, 75, 90, 110, 125, 140 mm, main clamp OD 160 mm.
Power requirements: 2.45 kW – Minimum required of a 3.5 kVA generator 240 V, single phase.
250 mm Butt Fusion Machine (Electric Hydraulic):
Buy this 250 mm butt fusion machine for welding HDPE pipes between 90 mm and 250 mm diameter in electric hydraulic mode. You may need a 5.9 kVA portable generator to power your poly welding equipment on site.
250 mm fusion welding machine hire comes complete with an extractable heating plate, extractable milling cutter, electro-hydraulic gear case, heating plate and cutter support, tool kit, and stub end device (spider).
** set of inserts OD 90, 110, 125, 140, 160, 180, 200, 225 mm, main clamp OD 250 mm.
Power requirements: 3.85 kW – Minimum required of a 5.9 kVA generator 240 V, single phase.
355 mm Butt Fusion Machine (Electric Hydraulic):
Purchase this 355 mm butt welder for HDPE welding of PE pipe between 90 mm and 355 mm diameter in electric hydraulic mode. Buy this fusion welder along with the 6.8 kVA portable generator – perfect for poly welding equipment being used on site.
TheHDPE butt fusion welding machine welder comes complete with an extractable heating plate, extractable milling cutter, electro-hydraulic gear case, heating plate and milling cutter support, tool kit, and stub end device (spider).
** set of inserts OD 90, 110, 125, 140, 160, 180, 200, 225, 250, 280, 315 mm, main clamp OD 355 mm.
Power requirements: 4.85 kW – Minimum required of a 6.5 kVA generator 240 V, single phase.
450 mm Butt Fusion Machine (Electric Hydraulic):
Buy the 450 butt fusion welding machine for butt-welding polyethylene pipes with an outside diameter between 200 mm and 450 mm diameter in electric hydraulic mode. Contact our team to hire a suitable generator, for butt welding in the field. The butt-welding machine includes a jib crane to assist with the milling cutter and heater plate, which are quite heavy due to the large capacity of the butt welder.
This but welder comes complete with an extractable heating plate, extractable milling cutter, electro-hydraulic gear case, heating plate and milling cutter support, tool kit, and stub end device (spider).
** set of inserts OD 200, 225, 250, 280, 315, 355, 400 mm, main clamp OD 450 mm
Power requirements: 8.38 kW – Recommended generator for field operation – 11 kVA 415 v, three phase.
630 mm Butt Fusion Machine (Electric Hydraulic):
The 630 butt welder machine is perfect for butt-welding HDPE pipes with an outside diameter between 315 mm and 630 mm diameter in electric hydraulic mode. Contact our team to hire or buy a suitable generator, for on-site butt welding.
The butt welding machine includes a jib crane to assist with the milling cutter and heater plate, which are quite heavy due to the large capacity of the butt welder.
When you buy this poly welding equipment, it includes an extractable heating plate, extractable milling cutter, electro-hydraulic gear case, heating plate and milling cutter support, tool kit, and stub end device (spider).
** set of inserts OD 315, 355, 400, 450, 500, 560 mm, main clamp OD 630 mm
Power requirements: 12.35 kW – Recommended generator for field operation – 16 kVA 415 V, three phase.
A1: A butt-fusion welding machine is a specialized equipment used in the joining of thermoplastic pipes, particularly in the fusion welding process known as butt fusion.
A2: Butt-fusion welding involves heating the ends of two thermoplastic pipes, allowing them to melt and then joining them together under pressure to create a seamless and strong connection.
A3: Butt-fusion welding machines are commonly used for joining pipes made of materials like High-Density Polyethylene (HDPE), Polypropylene (PP), and Polyvinyl Chloride (PVC).
A4: A typical butt-fusion welding machine consists of a heating plate, hydraulic system, facing tool, and a control unit to regulate temperature and pressure during the welding process.
A5: Butt-fusion welding machines are designed for specific pipe size ranges. Different machines cater to various diameters, ensuring compatibility with a wide range of pipe dimensions.
A6: The benefits of butt-fusion welding include creating strong and leak-free joints, ensuring a seamless connection, and maintaining the structural integrity of the pipe system.
A7: Butt-fusion welding is commonly used for pipes made of thermoplastics like HDPE, PP, and PVC. However, the suitability may vary based on specific pipe material and application requirements.
A8: Yes, butt-fusion welding is suitable for both above-ground and underground installations, providing flexibility in various construction scenarios.
A9: Safety measures include wearing appropriate protective gear, following manufacturer guidelines, and ensuring proper ventilation in the welding area to avoid exposure to fumes.
A10: Operator training is crucial to ensure proper handling of the equipment, accurate temperature and pressure control, and the creation of reliable and durable joints in the welding process.